|
Details |
Case Code: CLHR062
|
Case Length: 8 pages |
Period: 2007-2020 |
Pub Date: 2020 |
Teaching Note: Available |
Subject : Human Resources/ Organization Behavior |
Price:Rs.150 |
Organization :Bayerische Motoren Werke AG |
Industry :Automotive |
Countries : Germany |
|
|
|
Digitalization and People-oriented Production Systems at BMW |
|
|
The case `Digitalization and People-Oriented Production Systems at BMW` focuses on the role of technology and digitalization in enhancing job satisfaction and productivity with reference to the older workforce in the manufacturing sector. Bayerische Motoren Werke AG (BMW) was worried about its aging workforce. This was a cause for concern as older employees reported sick more frequently and for longer durations and had to work harder to achieve the same output as younger employees on the production floor. Sacking or reallocating older employees was not an option for the company because of the lack of young workers in Germany. Besides, BMW believed that its older workers were worth retaining for their maturity, extensive knowledge, reliability, and skills, and that they would remain productive and happy if they were provided on-the-job aids that made demanding and repetitive assembly line work less tiring and more convenient.BMW initiated an innovative bottom-up approach: 'Project production line 2017` in 2007 to tackle the issues faced by older employees. As part of the initiative, BMW decided to test its new approach at its Dingolfing facility in Germany that manufactured gearboxes. It staffed a production line with 42 employees with an average age of 47 years that was indicative of the plant's projected demographic makeup of 49 years in 2017. At the beginning there was strong resistance from other workers at the facility. Younger workers feared that they would suffer from the lower productivity of older workers. The older workers, on their part, feared that they would become less productive, as they would have to now perform tasks outside their comfort zones. The senior management and technical experts organized workshops and surveys and encouraged employees to contribute their ideas and also helped implement some of them. The focus was on work place design and production ergonomics. In total, more than 70 changes were implemented. Some of the initiatives such as Exoskeleton 'chairless chair', ProGloves, Ergonomic workwear, and Context-sensitive assistance systems were later extended to BMW`s other manufacturing facilities. Digitalization for the future work place or Industry 4.0 was another focus area of the company. The group adopted digital technologies that would reduce the stress of senior as well as regular employees and enable them handle complex tasks. Innovative automation technologies and smart tools, additive manufacturing, the use of automated data analysis, and smart data technologies for logistics were the focus areas of the digitalization initiative. BMW`s initiatives helped the company surmount the challenges of an aging workforce and also to leverage the benefits of digitalization implemented in its manufacturing facilities. The productivity of senior employees improved and was close to that of the younger ones; absenteeism related to sick leave declined; and the costs of preventive health care and rehabilitation did not increase drastically. |
Buy Now |
To download this case click on the button below, and select the case from the list of available cases: |
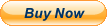
OR
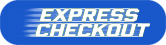 |
|
|
|
Issues: |
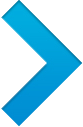 |
- Understand the importance of the older workforce in an organization.
|
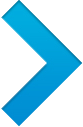 |
- Be aware of the need for technology innovation to retain an aging workforce
|
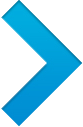 |
- Understand the link between technology, job satisfaction, and productivity.
|
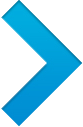 |
- Learn about digitalization and its positive impact on the workforce.
|
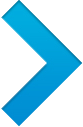 |
- Need for modernizing the work environment to increase workforce efficiency.
|
|
Introduction |
According to business intelligence portal Statista, the average age of Germany`s population was 46 years as of 2015. This was a steep increase from 40 in 2000 and 34 in 1970. A study by the Bertelsmann Foundation calculated that by 2020, three workers would support every person in Germany aged over 65, but this would become one-to-one by 2035. A German aged 65 was expected to live about another 20 years, according to recent OECD data. ... |
Keywords |
BMW; Older workers; Industrial Ergonomics; Digitalization; Work Stress; Automation; Smart Tools; Industry 4.0; Job satisfaction; Job attitudes; Diversity Management; Human Machine Interaction; Assembly Line Productivity; Smart Logistics; Additive Manufacturing
* This caselet is intended for use only in class discussions.
** More comprehensive case studies are priced at Rs.200 to Rs.700 (US $5 to US
$16) per copy.
|
|
|
|